Navigating the world of pharmaceutical assembly equipment can be overwhelming. With many options available, it's crucial to choose the right equipment tailored to your specific needs. In this guide, we'll break down key considerations to help you make an informed decision, ensuring optimal efficiency and safety in your operations.
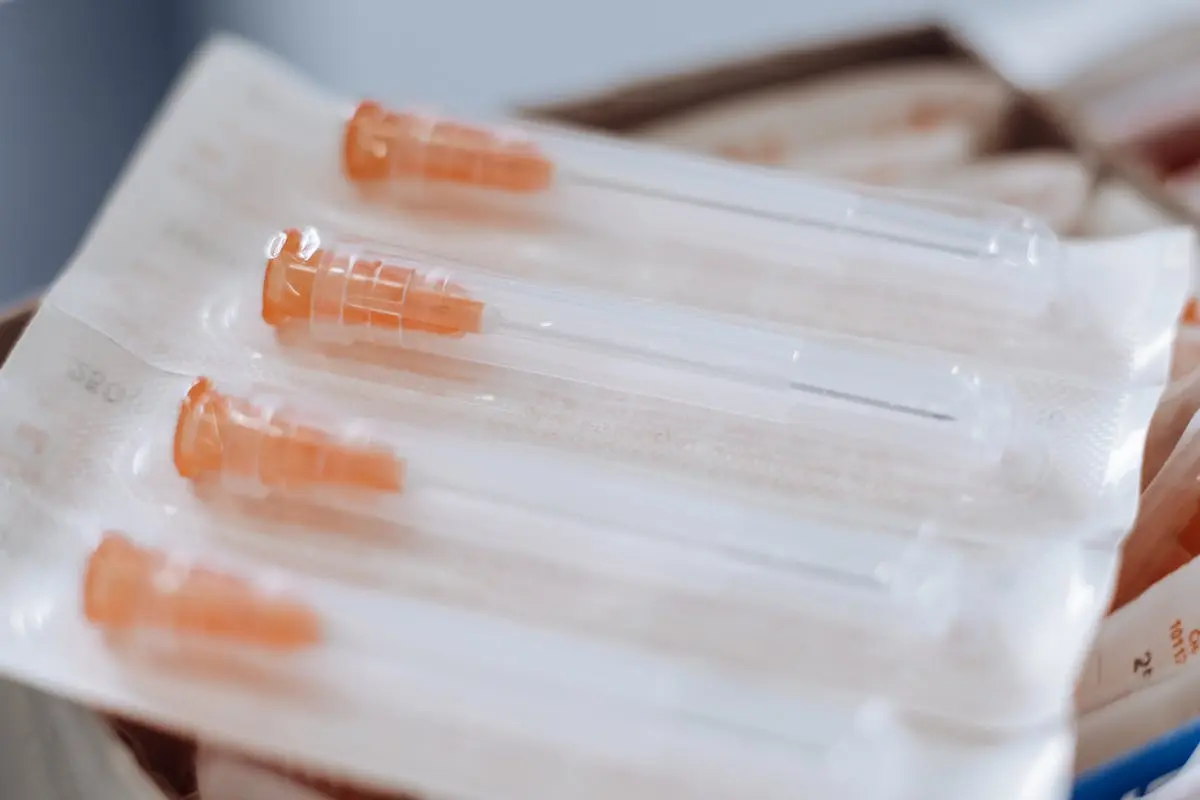
Understanding Your Pharmaceutical Production Needs
Before diving into equipment options, it's essential to assess your production needs. Consider the types of products you manufacture, production scale, and specific regulatory guidelines that apply.
Start by outlining your product categories. Are you producing liquids, solids, or perhaps a combination? Each product type has distinct requirements. For example, handling liquids often necessitates special filling machines with precise dispensing capabilities, while solid products may require more robust assembly lines.
The scale of production also plays a significant role. A small-scale operation might require different assembly technologies compared to a facility that manages large batches. Understanding whether your production will be continuous or in batches can guide you in choosing equipment that is not only efficient but also future-proof.
Additionally, keeping an eye on regulatory guidelines will help inform your decisions. Different products have varying compliance standards; always check that any potential equipment adheres to these regulations to safeguard your operation from unnecessary complications.
Key Features to Look for in Assembly Equipment
Not all assembly equipment is created equal. Look for features such as automation capabilities, ease of cleaning, and adaptability for various products to ensure you select equipment that meets your unique manufacturing requirements.
Automation can dramatically improve efficiency. Modern assembly lines are increasingly integrated with technology that reduces the need for manual input, allowing for quicker turnaround times. Look for equipment that can be programmed for various tasks, making it versatile enough to adapt to production changes.
Furthermore, consider the cleaning process of the equipment. In the pharmaceutical realm, sanitation is non-negotiable. Equipment that is designed with easy disassembly can make cleaning simpler and more effective, minimizing the risk of cross-contamination.
Adaptability is another crucial feature. As your product line evolves, the equipment will need to accommodate new formulations and packaging. Investing in modular machines that can be easily reconfigured will save time and money in the long run.
Evaluating Different Types of Assembly Equipment
From filling machines to labeling systems, each type of assembly equipment serves a specific purpose. Familiarize yourself with the various types available, and determine which will best fit into your production line.
Filling machines are an excellent starting point. They are essential for liquid products, where precision is critical. Explore options that come with advanced measurement technologies to ensure every unit is just right. If your production also includes solid dosage forms, consider equipment that can seamlessly transition between different types of products.
Labeling systems deserve special attention, as they are the final touch before your product reaches the consumer. A reliable labeling machine not only enhances brand visibility but must also comply with regulatory requirements. Make sure to research options that offer flexibility to handle various label shapes and sizes.
Don't overlook packaging equipment, which plays a vital role in preserving product integrity. Whether your products are being packaged in bottles, blister packs, or bulk containers, choosing the right system can impact your overall workflow efficiency.
Considering Compliance and Regulatory Standards
In the pharmaceutical industry, compliance is non-negotiable. Ensure that the equipment you choose adheres to relevant FDA guidelines and other industry regulations to avoid costly setbacks.
Each piece of equipment should come with robust documentation that proves its compliance status. This isn't just about following the rules; it's about commitment to quality and safety—a value that resonates deeply within the pharmaceutical landscape.
Regular audits can also help in maintaining compliance. Equipment should be evaluated not only at the point of purchase but continuously throughout its lifecycle. Ensure whoever you buy from offers good after-sales support, which will be crucial for any necessary recalibrations or upgrades.
Understanding compliance shouldn’t be a burden; rather, see it as integral to manufacturing excellence. By prioritizing regulatory criteria, you lay the groundwork for trust with consumers, regulators, and stakeholders alike.
Determining Your Budget and Investment Potential
Budgeting for pharmaceutical assembly equipment involves both initial investment and ongoing maintenance costs. Examine your financial capabilities and evaluate equipment that offers the best return on investment while staying within budget.
Start by understanding your total cost of ownership. It’s essential to factor in not just the purchase price but also operational costs, maintenance, and potential downtime. Sometimes, spending a little more upfront can yield significant savings on maintenance and repairs later.
Consider different financing options as well. Many manufacturers offer leasing or financing programs that can help spread the cost over time. This can ease budgeting pressures and enable you to invest in higher-quality equipment without straining your immediate funding.
Moreover, weigh the long-term benefits over short-term savings. Investing in high-quality equipment that enhances productivity and compliance can uplift your entire operation, maximizing profitability in the long run.
Seeking Expert Advice and Support
Don't hesitate to reach out for expert advice. Consulting with industry professionals can provide invaluable insights and help you navigate the complexities of choosing the right equipment.
Consider joining industry forums or networks where you can engage with peers facing similar challenges. Collective experiences often reveal common pitfalls and best practices that can guide your equipment selection.
Vendor assessments are equally important. Don’t merely take a salesperson’s word for it—ask for case studies, customer testimonials, and examples of successful implementations. This kind of due diligence can illuminate the best choices for your specific needs.
Lastly, don't overlook training and support from equipment suppliers. A solid training program ensures that your team can operate the machinery efficiently, reducing errors and increasing productivity right from the start.
Final Thoughts on Selecting Pharmaceutical Assembly Equipment
Choosing the right pharmaceutical assembly equipment is essential for streamlining processes while maintaining quality and compliance. By understanding your specific requirements, evaluating available equipment, and seeking expert advice when necessary, you can make a well-informed choice that enhances your productivity and meets industry standards.