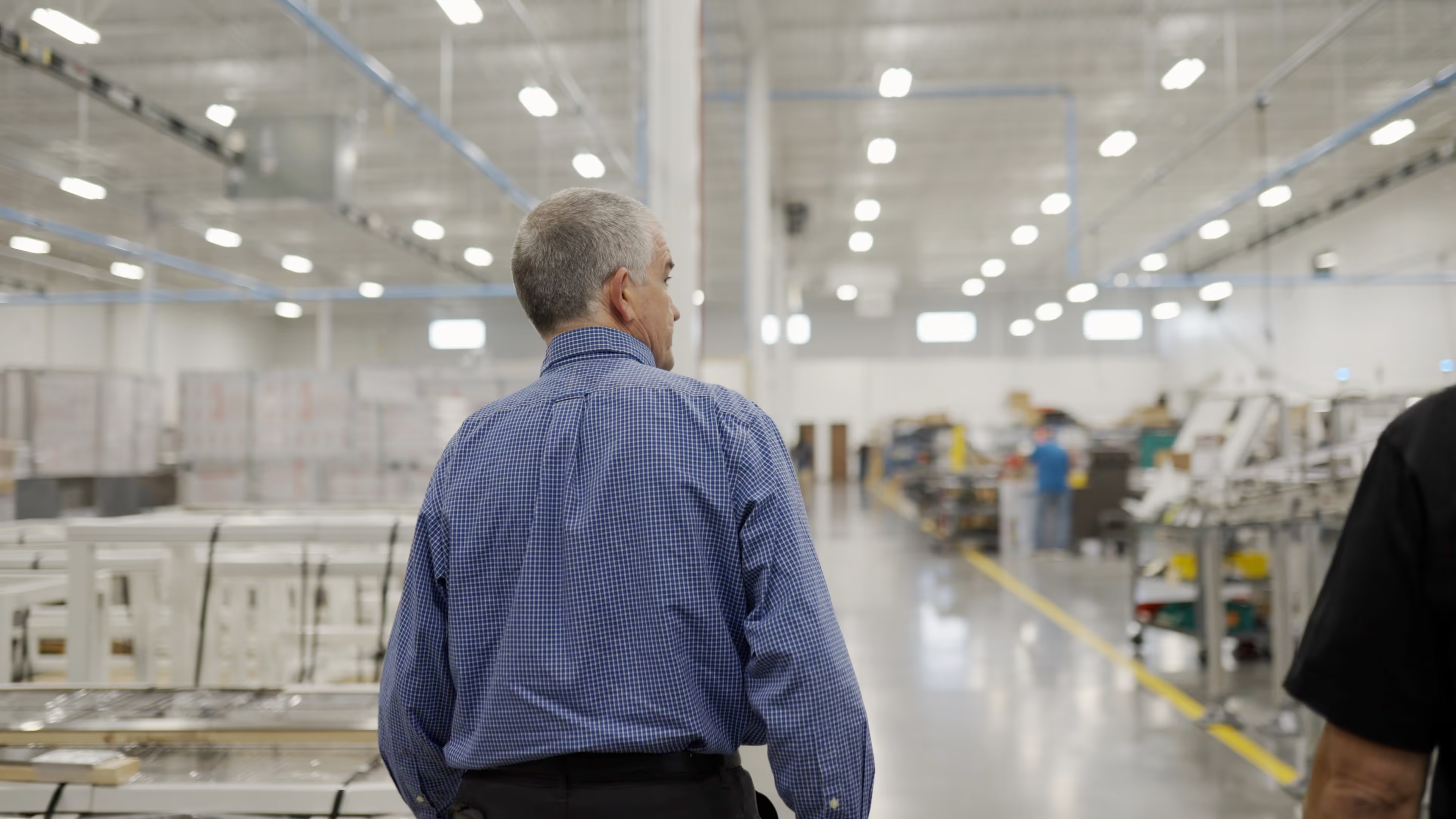
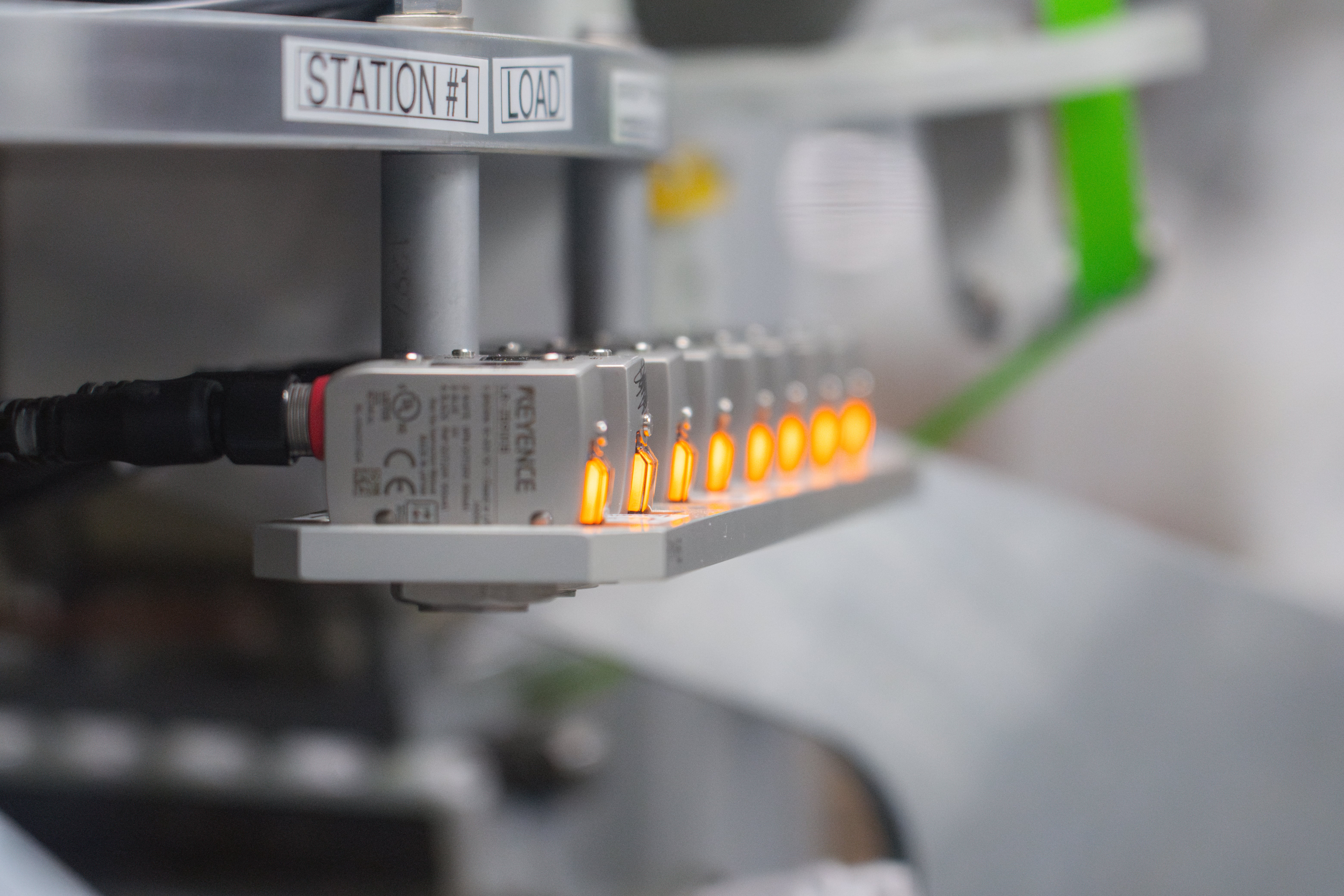
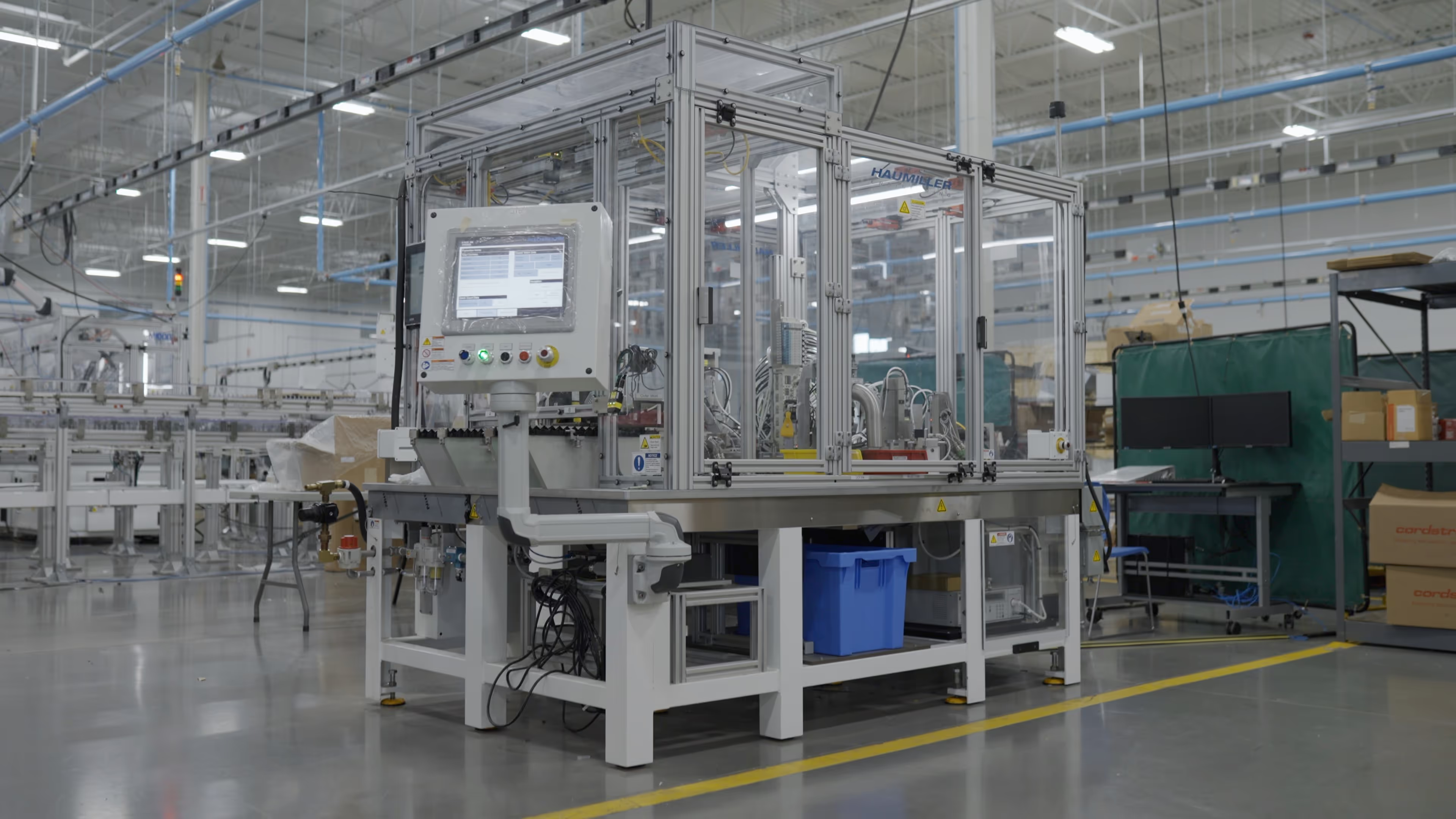
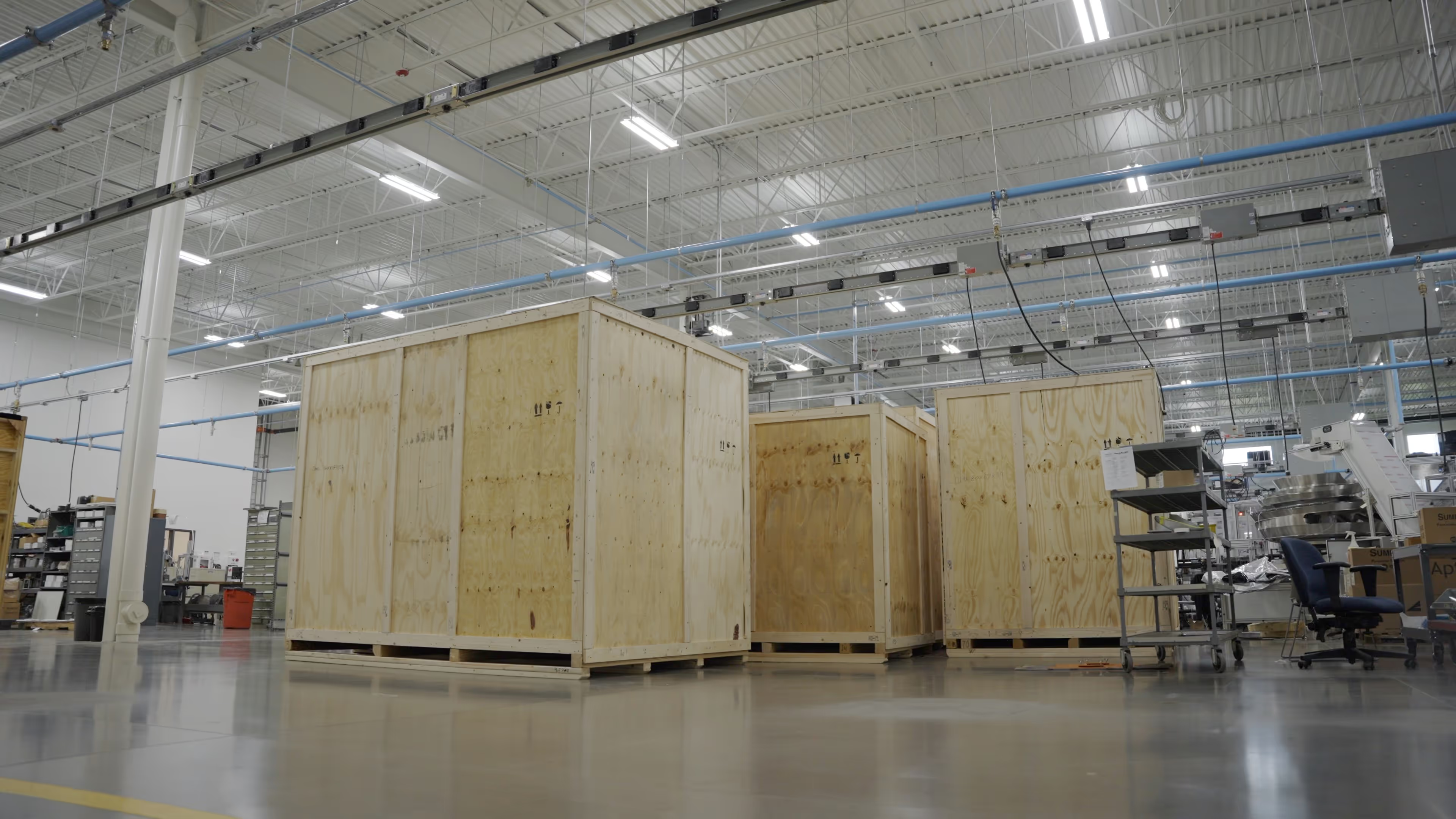
Designing a high-speed assembly system while developing your product presents inherent risks. With over 60 years of experience, Haumiller mitigates these risks by working closely with your team to:
By integrating concurrent engineering into your product design process, we help improve:
High-speed continuous motion assembly requires precise part dimensions. By understanding variations like flash or warpage early, we design systems to accommodate the required tolerances.
We help reduce time-consuming changeovers by incorporating subtle design features that increase compatibility between product sizes.
Common issues like nesting or part locking in feed systems can slow down production. We assess potential constraints and suggest modifications—such as internal or external ribs—to prevent parts from wedging together.
If parts have sensitive areas (such as fluid paths) that shouldn’t be touched, we work around those restrictions early to ensure your system maintains quality and precision.
By defining quality specifications upfront, we develop inspection systems that efficiently identify and remove defective parts without slowing down production.
Partnering with Haumiller means adding automation experts to your team who optimize not only your assembly system but also the quality of your end product. The result?
Contact us to discuss your project parameters and see how concurrent engineering can streamline your production process.
We believe in the power of teamwork and collaboration.
Our testing team isn't trying to make the machine work—they're trying to make the machine fail. We assess the durability of every machine to ensure your machine will last with any operator under any condition.
A series of short tests of every separate function of the machine to find obvious errors while running only the specific parts, and is completed when each function of the machine has run approximately 10 seconds.
Phase 2 is a series of tests, operating the machine as a whole interactive system. It is completed when the machine has run approximately 5 consecutive minutes with every function working.
A test of each specified set of parts, with every function working and the machine operating as a complete, interactive system. This phase is considered complete when the machine has run satisfactorily for 30 consecutive minutes unless a different time frame is specified.
At Haumiller Engineering, we specialize in designing and developing custom automation systems that seamlessly integrate into various industrial processes. Our expertise lies in crafting unique solutions that cater to your specific needs, ensuring precision, efficiency, and cutting-edge design.